High-Quality Hand Forged Wrought Iron Hooks for Sale
By:Admin
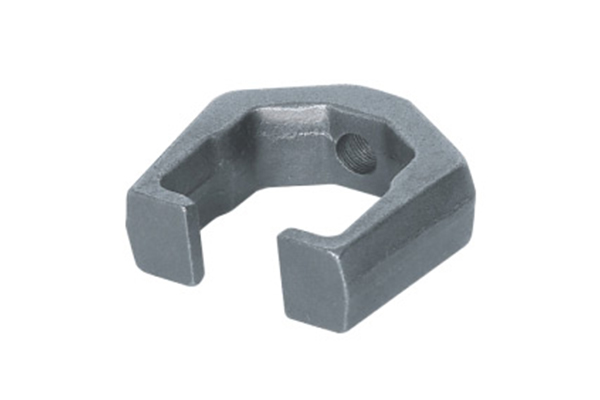
The art of blacksmithing is a tradition that dates back to ancient times, and it involves shaping and manipulating iron with the use of heat and force. Each piece that is hand forged by skilled blacksmiths is unique and carries with it a sense of artistry and authenticity that cannot be replicated by mass production methods. {}
{} has upheld this tradition and has dedicated themselves to producing the highest quality hand forged wrought iron hooks on the market. Their hooks are meticulously crafted using traditional blacksmithing techniques, resulting in durable and visually appealing pieces that are sure to enhance any space.
The company's commitment to quality is evident in every aspect of their production process. From sourcing the finest materials to employing highly skilled blacksmiths, {} ensures that each hook meets their exacting standards. The result is a product that not only serves a practical purpose but also serves as a work of art that can be appreciated for generations to come.
One of the hallmarks of {} is their diverse range of hand forged wrought iron hooks. Whether it's for hanging coats, towels, or kitchenware, their collection offers a wide variety of styles and sizes to suit any need. From classic and traditional designs to more contemporary and sleek options, {} has something for everyone. Their hooks are not only functional but also add a touch of vintage charm and elegance to any space.
In addition to their wide selection, {} also offers custom design services for those looking for a one-of-a-kind piece. Their team of skilled artisans can work closely with clients to bring their unique vision to life, ensuring that each custom piece is crafted with the same level of care and attention to detail as their standard line of hooks.
It's not just the quality of their products that sets {} apart, but also their commitment to customer satisfaction. The company understands the importance of providing exceptional service and support to their clients, and they strive to make the buying process as seamless and enjoyable as possible. From the initial inquiry to the final delivery, {} works diligently to ensure that each customer's needs are met with the highest level of professionalism and care.
In addition to their dedication to craftsmanship and customer service, {} is also committed to sustainability and ethical business practices. They prioritize using environmentally friendly materials and processes, and they work to minimize their environmental impact at every stage of production. By choosing {}'s hand forged wrought iron hooks, customers can feel good knowing that they are supporting a company that values both quality and sustainability.
In conclusion, {} has solidified their reputation as a leading provider of hand forged wrought iron hooks through their unwavering commitment to quality, craftsmanship, and customer satisfaction. With a diverse range of products, custom design options, and a dedication to sustainability, they continue to uphold the timeless tradition of blacksmithing while meeting the modern demands of today's consumers. Whether it's for practical use or as a statement piece, {}'s hooks are sure to leave a lasting impression in any home or space.
Company News & Blog
Ultimate Guide to Die Forging: Process, Benefits, and Applications
Die Forging is a manufacturing process that has been around for centuries and is still widely used today to create high-strength, complex metal components. This process involves shaping metal blanks using a die, or a specialized tool, to achieve the desired shape and size. The result is a component with excellent mechanical properties and uniform grain structure, making it ideal for critical applications in industries such as automotive, aerospace, and defense.{Company name} is a leading global manufacturer specializing in die forging, with a long history of delivering high-quality forged components to a wide range of industries. With state-of-the-art facilities and a skilled workforce, {Company name} has established itself as a trusted partner for companies looking for precision-engineered components that meet the highest standards of performance and reliability.The die forging process at {Company name} begins with carefully selected raw materials, often high-quality steel or aluminum alloys, which are heated to a specific temperature to enhance their plasticity. The heated metal blanks are then placed into a die, where immense pressure is applied to shape them into the desired form. This process ensures the final components have a fine-grained microstructure and exceptional mechanical properties, including high tensile and yield strength, excellent fatigue resistance, and superior impact toughness.One of the key advantages of die forging is the ability to produce components with complex geometries and intricate details, all while maintaining tight tolerances and superior surface finish. This makes die forging an excellent choice for parts that require high precision and reliability, such as gears, shafts, connecting rods, and other critical automotive and aerospace components.In addition to its manufacturing capabilities, {Company name} also offers a range of secondary operations to further enhance the performance and functionality of its forged components. These operations can include heat treatment to improve the material's properties, precision machining to achieve tight dimensional tolerances, and surface treatments to enhance corrosion resistance and wear characteristics.{Company name} has developed a reputation for excellence in die forging, driven by its commitment to continuous improvement and innovation. The company invests in advanced technologies and equipment to ensure that its manufacturing processes remain at the forefront of the industry, enabling it to meet the evolving needs of its customers and deliver components that exceed expectations.Furthermore, {Company name} follows stringent quality control procedures at every stage of the die forging process, from material inspection to final inspection, to ensure that its products consistently meet the highest standards of quality and performance. This commitment to quality has earned {Company name} various industry certifications, establishing it as a reliable and reputable supplier in the global marketplace.As the demand for lightweight, high-strength components continues to grow across various industries, die forging remains a preferred manufacturing process for achieving these characteristics. With its extensive experience and expertise, {Company name} is well-positioned to meet this increasing demand and provide innovative solutions to its customers' most challenging engineering requirements.In conclusion, die forging is a critical manufacturing process that plays a vital role in producing high-quality, high-performance components for a wide range of industries. {Company name} has established itself as a leader in the die forging industry, delivering precision-engineered components that meet the strictest standards of quality and performance. With its advanced manufacturing capabilities, commitment to innovation, and dedication to excellence, {Company name} continues to be a trusted partner for companies seeking reliable and high-quality die-forged components.
Innovative Multi-Directional Forging: A Breakthrough in Metalworking Technology
Multi-Directional Forging Revolutionizes Metal ManufacturingIn today's fast-paced and ever-evolving industrial landscape, the demand for innovative and efficient metal manufacturing solutions has never been higher. With increasing pressure to produce high-quality, durable metal components at a rapid pace, manufacturers are constantly seeking new technologies to streamline their processes and stay ahead of the competition.One company at the forefront of this technological revolution is {}. With over three decades of experience in the metal forging industry, {} has recently introduced a game-changing technology known as Multi-Directional Forging (MDF). This cutting-edge technique has quickly gained recognition for its ability to produce high-strength, complex metal components with unmatched precision and efficiency.Traditional forging methods typically involve the use of dies and hammers to shape metal into the desired form. While effective, these methods are often limited in their ability to produce intricate shapes and precise details. This is where MDF comes in, offering a revolutionary approach to metal forming that has the potential to completely transform the industry.MDF utilizes a unique process that involves applying pressure to metal billets from multiple directions simultaneously. This multi-directional force allows for greater control over the shaping process, resulting in components with superior mechanical properties and a higher degree of accuracy. By exerting pressure from all sides, MDF eliminates the need for multiple forging operations, reducing production time and costs while improving overall product quality.One of the key advantages of MDF is its ability to produce near-net-shape components, significantly reducing the amount of material that needs to be machined away. This not only minimizes waste but also leads to substantial cost savings for manufacturers. Additionally, the enhanced mechanical properties of MDF components make them ideal for applications requiring high strength and durability, such as automotive and aerospace industries.The development of MDF is a testament to {}'s commitment to innovation and excellence in metal forging. As a leading provider of metal components to a wide range of industries, {} has consistently invested in cutting-edge technologies to meet the evolving needs of its customers. The introduction of MDF further solidifies {}'s position as a pioneer in the industry, setting new standards for precision and performance in metal manufacturing.Beyond the technological advancements, {}'s dedication to sustainability and responsible production is evident in its adoption of MDF. By minimizing material waste and energy consumption, MDF aligns with {}'s commitment to environmentally friendly manufacturing practices, further enhancing its reputation as an industry leader in corporate social responsibility.With the introduction of Multi-Directional Forging, {} is poised to revolutionize the metal manufacturing industry and set new benchmarks for quality, efficiency, and sustainability. As demand for high-performance metal components continues to grow, MDF's potential to deliver superior products in a cost-effective and sustainable manner makes it a game-changing solution for manufacturers worldwide.As the industry embraces the era of digital transformation, {} remains at the forefront, driving innovation and shaping the future of metal manufacturing. With Multi-Directional Forging, {} is not only revolutionizing its own operations but also empowering its customers to stay ahead in an increasingly competitive market. As the global manufacturing landscape continues to evolve, {}'s pioneering approach to metal forging ensures that the company remains a trusted partner for cutting-edge solutions and unparalleled quality.
How to Use a Casting Kit: Step-by-Step Guide for Creating a Perfect Mold at Home
Casting Kit, a leading provider of professional casting supplies and equipment, has recently introduced a new casting kit that is designed to revolutionize the way artists and enthusiasts create their own metal castings. The company, known for its commitment to quality and innovation, has developed a comprehensive kit that includes everything needed to create high-quality metal castings in the comfort of one's own home or studio.The new casting kit includes a variety of essential tools and materials, including a crucible, tongs, safety equipment, and a high-quality furnace. The kit also includes a detailed instructional guide that provides step-by-step guidance on the casting process, making it suitable for both beginners and experienced casters. With this comprehensive kit, artists can now create their own metal castings with ease and precision, without the need for expensive equipment or specialized training."We are thrilled to introduce our new casting kit, which has been designed to meet the needs of artists and creators who are passionate about metal casting," said [Spokesperson name], the founder and CEO of Casting Kit. "We believe that everyone should have the opportunity to explore their creativity and create their own metal castings, and our new kit makes that possible. Whether you are a seasoned metal caster or a complete beginner, our kit provides everything you need to get started and unleash your creativity."In addition to providing a comprehensive casting kit, Casting Kit also offers a wide range of professional-grade casting supplies and equipment, all of which are designed to meet the highest standards of quality and performance. The company's extensive product line includes crucibles, molds, sand casting tools, and other essential casting accessories. Whether customers are looking to create intricate jewelry pieces, artistic sculptures, or functional metal parts, Casting Kit offers the tools and materials needed to bring their visions to life.Casting Kit also provides an array of resources and support to help customers succeed in their metal casting endeavors. The company's website features an extensive library of instructional articles, videos, and tutorials that cover a wide range of casting techniques and best practices. Additionally, Casting Kit's team of experienced casting professionals is available to provide personalized guidance and assistance to customers, ensuring that they have everything they need to achieve their casting goals."We are more than just a supplier of casting supplies – we are a partner to our customers, empowering them with the knowledge, tools, and support they need to succeed in their casting projects," said [Spokesperson name]. "Our goal is to make metal casting accessible to everyone, and we are committed to providing the highest quality products and resources to support our customers every step of the way."As the demand for metal casting continues to grow among artists, makers, and hobbyists, Casting Kit remains at the forefront of the industry, continually innovating and expanding its product offerings to meet the evolving needs of its customers. With its new casting kit and comprehensive range of casting supplies and equipment, Casting Kit is well-positioned to empower a new generation of metal casters and creators, helping them unleash their creativity and bring their visions to life.For more information about Casting Kit and its comprehensive range of casting supplies and equipment, please visit [website].
Top Techniques for Forging Intermediate Rocker
Forging Intermediate Rocker, a process used by the leading outdoor equipment company, {company name}, has revolutionized the way rockers are made for outdoor sports equipment. This innovative technique has set a new standard for durability and performance in the industry, making {company name} a frontrunner in the outdoor equipment market.The Forging Intermediate Rocker process involves shaping and molding metal into the desired rocker shape by using high-pressure forging techniques. This results in a superior strength-to-weight ratio, making the rockers incredibly durable and able to withstand the demanding conditions of outdoor sports such as hiking, climbing, and trail running. The technique also allows for precise control over the shape and design of the rockers, optimizing their performance for various outdoor activities.{company name} has been at the forefront of innovation in outdoor equipment manufacturing for over a decade. With a commitment to quality and performance, the company has consistently pushed the boundaries of traditional manufacturing techniques to create products that exceed the expectations of outdoor enthusiasts. The introduction of Forging Intermediate Rocker is just one example of {company name}'s dedication to advancing the industry and providing customers with the best possible gear for their outdoor adventures.The Forging Intermediate Rocker process has been integrated into a range of {company name}'s outdoor equipment, including hiking boots, trail running shoes, and climbing gear. By utilizing this innovative technique, {company name} has been able to enhance the performance of these products, making them more durable, responsive, and reliable in the rugged outdoor environments where they are used. This has solidified {company name}'s position as a leader in the outdoor equipment market, setting them apart from competitors and earning them a loyal customer base.In addition to the performance benefits of Forging Intermediate Rocker, {company name} has also prioritized sustainability and environmental responsibility in its manufacturing processes. By optimizing the use of materials and minimizing waste, the company has minimized its environmental impact while still delivering high-quality, long-lasting products to its customers. This commitment to sustainability has resonated with environmentally conscious outdoor enthusiasts, further enhancing {company name}'s reputation as a trusted and responsible outdoor equipment manufacturer.As {company name} continues to innovate and push the boundaries of outdoor equipment manufacturing, the introduction of Forging Intermediate Rocker has solidified their position as a leader in the industry. By utilizing this innovative technique, the company has been able to create rockers that are not only incredibly durable and reliable but also optimized for performance in a variety of outdoor activities. This has set a new standard for rockers in the outdoor equipment market, cementing {company name}'s reputation as a frontrunner in the industry.Overall, the introduction of Forging Intermediate Rocker by {company name} has been a game-changer in the outdoor equipment market. This innovative technique has set a new standard for durability and performance in rockers, and has solidified {company name}'s position as a leader in the industry. With its commitment to quality, performance, and sustainability, {company name} continues to push the boundaries of outdoor equipment manufacturing, providing customers with the best possible gear for their outdoor adventures.
Benefits and Process of Pressure Casting in Manufacturing
Pressure Casting is a pivotal process for manufacturing various components used in a wide range of industries, including automotive, aerospace, and consumer goods. The process involves injecting molten metal into a mold cavity under high pressure, resulting in high-quality, detailed, and accurate components.One of the leading providers of Pressure Casting technology is {}. With a strong emphasis on innovation and delivering cutting-edge solutions, {} has earned a reputation as a trusted partner for companies seeking high-quality components for their products.Established in {}, {} has continually pushed the boundaries of Pressure Casting technology, investing in state-of-the-art equipment and processes to ensure the highest level of precision and efficiency in their manufacturing operations. Their team of experienced engineers and technicians work closely with clients to develop custom solutions that meet the specific requirements of each project.The company's commitment to excellence is evident in their rigorous quality control processes, where every component produced undergoes thorough inspection and testing to ensure it meets the highest standards. This dedication to quality has earned {} the trust of numerous clients, who rely on them to deliver components that are essential to the performance and reliability of their products.In addition to their focus on quality, {} is also dedicated to sustainability and environmental responsibility. They have implemented eco-friendly practices throughout their operations, from reducing waste and energy consumption to utilizing recyclable materials whenever possible. This commitment to sustainability has not only benefited the environment but has also provided cost-saving opportunities for their clients.Furthermore, {} has a strong emphasis on research and development, constantly seeking new materials and technologies to improve their Pressure Casting capabilities. This dedication to innovation has allowed them to stay at the forefront of the industry, offering their clients the most advanced solutions for their manufacturing needs.The company's impressive portfolio includes a wide variety of components, from intricate parts for automotive applications to critical components for aerospace and defense. Their expertise in Pressure Casting has made them a go-to partner for companies looking for reliable and high-quality components that meet the most demanding specifications.With a strong presence in the global market, {} has built a solid reputation for delivering on their promises, meeting deadlines, and providing exceptional customer service. Their commitment to excellence has earned them long-standing relationships with clients across various industries, who continue to rely on them for their Pressure Casting needs.Looking ahead, {} is poised to continue leading the way in Pressure Casting technology, with a focus on expanding their capabilities and exploring new opportunities for growth. Their dedication to innovation and commitment to quality ensure that they will remain a key player in the industry for years to come.In conclusion, Pressure Casting is a crucial process for manufacturing high-quality components, and with its dedication to excellence, innovation, and sustainability, {} is at the forefront of providing cutting-edge solutions to clients across a wide range of industries. As the company continues to push the boundaries of Pressure Casting technology, it is likely to remain a trusted partner for companies seeking top-of-the-line components for their products.
Quality Forged Automobile Parts: Why Forging is Important for Vehicle Components
The automotive industry is constantly evolving, and with advancements in technology and materials, the demand for high-quality and precision engineered automobile parts is greater than ever. One company that has been at the forefront of forging automobile parts is {}.{} is a leading manufacturer of forged automobile components. With over 20 years of experience in the industry, they have established themselves as a reliable and innovative supplier to some of the world's most renowned automotive companies.The process of forging automobile parts involves shaping metal using localized compressive forces. This results in parts that are stronger and more durable than those made through other manufacturing methods. {} has perfected the art of forging, using state-of-the-art technology and equipment to create components that meet the highest industry standards.One of the key factors that sets {} apart from its competitors is its dedication to research and development. The company has a team of engineers and technicians who are constantly working on improving their forging techniques, as well as developing new and innovative products. This commitment to innovation has allowed {} to stay ahead of the curve and continue to provide its customers with cutting-edge solutions.In addition to their focus on innovation, {} places a strong emphasis on quality control throughout the entire manufacturing process. Every step of the production is carefully monitored to ensure that the finished products meet the strictest performance and safety standards. This attention to detail has earned {} a reputation for delivering reliable and high-quality automobile parts.Another aspect that sets {} apart is its flexibility and ability to customize products to meet the specific needs of its customers. Whether it's a complex component for a luxury vehicle or a high-volume part for a mass-market car, {} has the expertise and capabilities to deliver tailor-made solutions to its clients.As the automotive industry continues to embrace advancements in technology, such as electric and autonomous vehicles, the demand for specialized and precision-engineered components is growing. {} has been quick to adapt to this changing landscape, and has expanded its product range to cater to the evolving needs of the industry.The company's commitment to sustainability is also worth mentioning. {} is dedicated to reducing its environmental impact by optimizing its manufacturing processes and using eco-friendly materials whenever possible. This focus on sustainability has not only benefited the environment, but has also allowed {} to stay ahead of regulatory requirements and meet the growing demand for environmentally conscious products.Looking toward the future, {} is poised to continue its growth and maintain its position as a leader in the forging automobile parts industry. With its unwavering dedication to quality, innovation, and customer satisfaction, {} is well positioned to meet the evolving needs of the automotive market and remain a trusted partner to its clients around the world.In conclusion, the automotive industry is constantly evolving, and {} continues to be a driving force in the development of high-quality and precision-engineered automobile parts. With its dedication to innovation, quality, flexibility, and sustainability, {} is well positioned to meet the demands of an ever-changing market and to continue to deliver top-notch products to its customers.
Customizable Lost Wax Steel Casting: What You Need to Know
Lost Wax Steel Casting: The Art of Precision ManufacturingIn the world of precision manufacturing, there are few processes as intricate and refined as lost wax steel casting. This centuries-old technique has been perfected by companies like [company name removed], and it continues to be a cornerstone of the modern manufacturing industry. With its roots in ancient Egypt and Mesopotamia, lost wax steel casting has evolved over the years to become one of the most precise and reliable methods for creating complex metal parts.[Company Name Removed] is a leader in the field of lost wax steel casting, with a reputation for producing high-quality, precision parts for a wide range of industries. Their state-of-the-art facilities and experienced team of engineers and craftsmen allow them to tackle even the most challenging casting projects with ease. From aerospace components to automotive parts, [company name removed] has the expertise and capabilities to meet the needs of their diverse customer base.The process of lost wax steel casting begins with the creation of a wax pattern of the desired part. This pattern is then coated with a ceramic material to create a mold that can withstand the high temperatures of the casting process. The wax is melted out of the mold, leaving behind a cavity in the exact shape of the original pattern. Molten steel is then poured into the mold, filling the cavity and taking on the precise form of the wax pattern. Once the steel has cooled and solidified, the ceramic mold is broken away to reveal the finished part, ready for further processing and finishing.One of the key advantages of lost wax steel casting is its ability to produce parts with intricate and complex shapes that would be difficult or impossible to create using other manufacturing methods. This makes it an ideal choice for industries that demand high precision and reliability, such as aerospace, defense, and automotive. [Company name removed]'s expertise in this area allows them to provide their customers with the high-quality parts they need to thrive in competitive markets.In addition to its precision and versatility, lost wax steel casting also offers cost savings and efficiency benefits. By allowing for tight tolerances and minimal material waste, this method of manufacturing can help companies reduce production costs while maintaining high quality standards. This makes it an attractive option for businesses looking to optimize their manufacturing processes and improve their bottom line.At [company name removed], the art of lost wax steel casting is complemented by a commitment to quality, innovation, and customer satisfaction. Their team works closely with each client to understand their unique needs and develop tailored solutions that meet and exceed expectations. Whether it's a one-off prototype or a large-scale production run, [company name removed] has the capabilities and expertise to deliver results that make a difference.With a dedication to continuous improvement and a focus on staying at the forefront of technological advancements, [company name removed] is poised to continue leading the way in the world of lost wax steel casting. Their ongoing investment in research and development, combined with their years of industry experience, ensures that they remain a trusted partner for companies seeking the highest standards of quality and precision in their manufacturing processes.As the demand for precision-engineered metal parts continues to grow across industries, the art of lost wax steel casting will only become more relevant and valuable. With [company name removed] at the helm, businesses can rest assured that they have a partner they can rely on to deliver the high-quality parts they need to succeed in today's competitive market.
Learn the Process of Sand Casting and Its Application in Manufacturing
Sand Casting Process: A Key Ingredient in {Company Name}'s Manufacturing ExcellenceSand casting is a widely used method for creating metal parts and components. It is one of the oldest known metal-forming techniques, with its origins dating back to ancient China. The process involves pouring molten metal into a sand mold, which is then allowed to cool and solidify, ultimately forming the desired shape.{Company Name} is a leading manufacturer in the industry, known for its expertise in utilizing sand casting to produce high-quality metal components for a variety of applications. The company's commitment to innovation and continuous improvement has made them a preferred choice for customers seeking precision components.The sand casting process begins with the creation of a pattern that matches the final product's shape. This pattern is typically made from wood, plastic, or metal and serves as a mold for the sand to be formed around. Once the pattern is prepared, it is placed into a box filled with fine sand, creating a cavity that matches the desired shape. The sand is then compacted around the pattern to ensure it maintains its form. Once the mold is ready, molten metal is poured into the cavity, and after it cools, the sand is broken away, revealing the finished component.{Company Name} has implemented state-of-the-art technology and modern manufacturing practices to enhance the efficiency and precision of the sand casting process. This allows them to produce intricate and complex components with tight tolerances, meeting the exact specifications of their customers.One of the key advantages of sand casting is its versatility. It can be used to create components of varying sizes and complexities, making it a cost-effective and flexible manufacturing solution. This, combined with the expertise and experience of {Company Name}, allows them to cater to diverse industries such as automotive, aerospace, energy, and more.Additionally, sand casting is known for its ability to produce components with excellent mechanical properties. The process allows for the use of a wide range of metals, including aluminum, iron, steel, and brass, providing customers with a myriad of options to meet their specific needs. As a result, {Company Name} has established itself as a reliable partner for customers looking for durable and high-performance metal components.In recent years, {Company Name} has made significant investments in research and development to further enhance the sand casting process. They have focused on improving mold design, material selection, and process optimization to minimize waste and maximize efficiency. These efforts have allowed them to maintain a competitive edge in the market while delivering superior products to their customers.Moreover, sustainability and environmental responsibility are core values for {Company Name}, and they have made a conscious effort to minimize the environmental impact of their manufacturing processes. The sand used in casting can be reused multiple times, and any excess sand is recycled, reducing waste and promoting a more eco-friendly approach to production.Looking ahead, {Company Name} remains committed to advancing its capabilities in sand casting and embracing new technologies to further elevate its manufacturing excellence. By continuously refining their processes and exploring new opportunities for innovation, they aim to stay at the forefront of the industry and continue to meet the evolving needs of their customers.In conclusion, sand casting is a cornerstone of {Company Name}'s manufacturing operations, playing a crucial role in their ability to deliver high-quality, precision components to a wide range of industries. With a dedication to innovation, efficiency, and sustainability, {Company Name} has solidified its position as a trusted partner for customers seeking superior metal components. As they continue to push the boundaries of what is possible with sand casting, the company is poised to remain a leader in the industry for years to come.
Durable and Versatile Stainless Steel Forging: A Complete Guide
Stainless Steel Forging: The Perfect Solution for Industrial ApplicationsStainless steel has become an essential material in various industries due to its exceptional properties, including corrosion resistance, durability, and strength. Its versatility makes it a popular choice for a wide range of applications, from automotive and aerospace to food processing and medical equipment.One of the key processes in manufacturing stainless steel components is forging. Forging involves shaping metal by applying force, typically using a hammer, press, or die. This process enhances the strength and toughness of the material, making it ideal for critical applications where reliability is paramount.In the world of stainless steel forging, one company that stands out is {}. With over 30 years of experience in the industry, {} has established itself as a leading manufacturer of high-quality forged stainless steel components. The company's dedication to precision, quality, and innovation has earned them a reputation for excellence among their clients.{} specializes in custom stainless steel forging, offering a wide range of shapes and sizes to meet the specific needs of their customers. Their state-of-the-art facilities and cutting-edge technology enable them to produce complex and intricate designs with unmatched precision and consistency.One of the key advantages of stainless steel forging from {} is the enhanced mechanical properties it provides. By subjecting the stainless steel to high levels of compressive force, the material's grain structure is refined, resulting in improved strength, ductility, and resistance to fatigue. This makes forged stainless steel components an ideal choice for demanding applications where safety and reliability are paramount.In addition to superior mechanical properties, stainless steel forging also offers excellent surface finish and dimensional accuracy. This ensures that the final components meet tight tolerances and specifications, making them suitable for use in critical industries such as oil and gas, power generation, and defense.The expertise and dedication of {} in stainless steel forging are evident in their commitment to quality and customer satisfaction. The company adheres to strict quality control measures throughout the forging process, ensuring that each component meets the highest standards of excellence. From raw material inspection to final inspection, {} employs rigorous testing and inspection procedures to guarantee the integrity and performance of their products.Furthermore, {} is dedicated to continuous improvement and innovation in their manufacturing processes. Their team of experienced engineers and metallurgists work collaboratively to develop new and advanced forging techniques, utilizing the latest technology and best practices to deliver cutting-edge solutions to their clients.Another notable aspect of {}'s stainless steel forging capabilities is their ability to work with a wide range of stainless steel grades. Whether it's austenitic, martensitic, or precipitation hardening stainless steel, {} has the expertise and resources to forge components from the most suitable material for the intended application.The company's dedication to sustainability and environmental responsibility is also evident in their manufacturing practices. {} employs efficient and eco-friendly processes in their forging operations, minimizing waste and energy consumption while maximizing the use of recyclable materials.To further enhance their customer service, {} offers comprehensive support and technical assistance to their clients, ensuring a smooth and seamless experience from design to production. Their team of experts is readily available to provide guidance and expertise, offering customized solutions to meet the unique requirements of each project.In conclusion, stainless steel forging from {} offers a multitude of benefits, making it the perfect solution for a wide range of industrial applications. As a leading manufacturer in the industry, {}'s dedication to quality, innovation, and customer satisfaction sets them apart as a trusted partner for those seeking high-quality forged stainless steel components. With their unwavering commitment to excellence, {} continues to drive the advancement of stainless steel forging, providing reliable and durable solutions for the most demanding applications.
High-Quality Metal Parts Washer for Efficient Cleaning Operations
The Metal Parts Washer is an innovative and essential tool for efficient and thorough cleaning and degreasing of metal parts. It is the latest product from our company, a leading manufacturer and supplier of industrial cleaning equipment. With a reputation for producing high-quality and reliable cleaning solutions for a wide range of industries, we are proud to introduce the Metal Parts Washer as the newest addition to our product line.The Metal Parts Washer is designed to meet the cleaning and degreasing needs of various industries, including automotive, aerospace, manufacturing, and more. It is equipped with advanced technology and features that make it a versatile and efficient solution for removing oil, grease, dirt, and other contaminants from metal parts. With its robust construction and user-friendly design, the Metal Parts Washer is built to withstand the demands of industrial cleaning operations and provide reliable performance for years to come.One of the key features of the Metal Parts Washer is its powerful pump and heating system, which ensures thorough cleaning and degreasing of metal parts. The pump delivers high-pressure cleaning solution to effectively remove tough contaminants, while the heating system helps to enhance the cleaning process and improve overall efficiency. Additionally, the Metal Parts Washer is equipped with a filtration system to keep the cleaning solution clean and prolong its life, reducing the need for frequent replacements.In addition to its advanced cleaning capabilities, the Metal Parts Washer is also designed with user convenience and safety in mind. It features a spacious and ergonomic work area, allowing for easy loading and unloading of parts, as well as a transparent viewing window for monitoring the cleaning process. The washer also comes with safety features such as automatic shut-off valves and overheat protection to ensure safe and reliable operation.The Metal Parts Washer is available in a range of sizes and configurations to meet the specific needs of different industries and applications. Whether it's for small-scale workshop operations or large industrial facilities, our company offers a comprehensive range of Metal Parts Washers to cater to diverse cleaning requirements and production volumes. Furthermore, our team of experts can provide customized solutions and technical support to help customers select the right washer for their specific needs and integrate it seamlessly into their operations.As a company, we are committed to delivering exceptional quality and performance with our products, and the Metal Parts Washer is no exception. Each washer undergoes rigorous testing and quality assurance processes to ensure that it meets the highest standards of reliability and efficiency. Additionally, our dedication to customer satisfaction extends to our after-sales service, with comprehensive support and maintenance services available to keep our customers' Metal Parts Washers running at peak performance.In conclusion, the Metal Parts Washer is a cutting-edge solution for industrial cleaning and degreasing of metal parts, designed and manufactured by our company to meet the diverse needs of various industries. With its advanced features, user-friendly design, and exceptional performance, the Metal Parts Washer represents the latest innovation in our commitment to delivering top-quality cleaning solutions. Whether it's for automotive, aerospace, manufacturing, or any other industry, the Metal Parts Washer is the ideal choice for efficient and reliable metal parts cleaning and degreasing. With our company's expertise and support, customers can trust in the Metal Parts Washer to meet their cleaning needs and contribute to their operational excellence.