Discover the Advantages of Hydraulic Forging for Precision Manufacturing
By:Admin
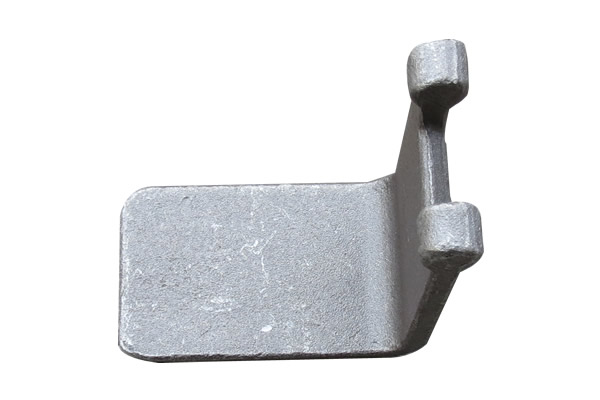
One company that has been at the forefront of hydraulic forging is {}. With over 50 years of experience in the industry, {} has established itself as a leader in the field of metal forging and manufacturing. The company prides itself on its commitment to innovation, quality, and customer satisfaction, and has continually invested in state-of-the-art equipment and technology to meet the ever-evolving needs of its clients.
One of the key advantages of hydraulic forging is the ability to produce complex and intricately shaped metal components with minimal material waste. By applying high-pressure hydraulic force to the metal, {} is able to create products with superior strength and durability. This makes hydraulic forged components highly desirable for use in critical applications such as aerospace, automotive, and defense industries.
In addition to its precision and strength, hydraulic forging also offers cost savings and environmental benefits. The process requires less material and energy compared to traditional forging methods, resulting in reduced waste and lower carbon emissions. This aligns with {}'s commitment to sustainable and environmentally-friendly manufacturing practices.
Moreover, hydraulic forging is capable of producing components in a wide range of sizes and shapes, from small intricate parts to large structural components. This versatility makes it an attractive option for a diverse array of industries, and {} has successfully catered to the needs of clients in sectors such as oil and gas, transportation, and construction.
With the increasing demand for lighter, stronger, and more durable metal components, the market for hydraulic forged products is expected to grow significantly in the coming years. Recognizing this trend, {} has continued to invest in its hydraulic forging capabilities, expanding its production capacity and enhancing its technological expertise to meet the evolving needs of its customers.
The company's dedication to quality and innovation has also been recognized through various certifications and accreditations, further solidifying its position as a trusted partner for hydraulic forging solutions. Its adherence to strict quality control measures and industry standards ensures that the products delivered to clients meet or exceed their expectations.
In conclusion, hydraulic forging is a cutting-edge manufacturing process that has become indispensable in the production of high-quality metal components. With its precision, strength, cost savings, and environmental benefits, it offers a compelling solution for a wide range of industries. As a leading player in the field, {} is well-equipped to meet the growing demand for hydraulic forged products and continue to drive innovation and excellence in metal forging and manufacturing.
Company News & Blog
Increase Your ROI with Investment Castings
Investment Castings: Combining Precision and Quality ManufacturingInvestment casting is a highly specialized manufacturing process used to create complex and intricate metal components, valued for their precision, fine surface finish, and dimensional accuracy. These high-quality castings find applications in various industries, including aerospace, automotive, energy, and medical devices, among others. Investment castings offer unique advantages over other manufacturing methods, making them the go-to choice for companies seeking superior quality and design flexibility.In this era of constant innovation and technological advancements, investment casting has evolved into a highly sophisticated manufacturing process. It involves creating a wax pattern of the desired component, which is then coated with a ceramic slurry and allowed to dry. The dried ceramic shell is then heated to remove the wax, leaving behind an empty cavity in the shape of the desired component. Molten metal is then poured into this cavity, filling the intricate details and contours perfectly. Once the metal solidifies, the ceramic shell is broken or dissolved, revealing the final investment casting.The investment casting process allows for the production of complex components with exceptional dimensional accuracy and near-net shapes. The versatility of the process enables the manufacturing of parts with intricate details, thin walls, and undercuts that would be challenging or even impossible to produce with other manufacturing techniques. This makes investment castings ideal for industries that require complex and intricate components, such as turbine blades, medical implants, or even intricate jewelry.One of the leading investment casting companies, {}, has been at the forefront of the industry for many years. Specializing in high-quality investment castings, the company has gained a reputation for delivering precision components that meet the most demanding requirements of its customers.With a state-of-the-art facility and a team of highly skilled engineers and technicians, {} has been able to push the boundaries of what investment castings can achieve. The company has invested heavily in advanced technology and equipment, enabling them to produce castings with unparalleled precision and surface finish. Their commitment to stringent quality control measures ensures that each casting produced meets the highest standards, surpassing customer expectations.{} boasts an extensive portfolio of successful projects across various industries. They have collaborated with leading aerospace manufacturers to produce intricate turbine blades and engine components that withstand extreme conditions while maintaining optimal performance. In the medical field, they have played a vital role in the production of implants and surgical instruments that require high precision and biocompatibility. Additionally, {} has partnered with automotive companies to create lightweight, yet durable castings that improve fuel efficiency and reduce emissions.What sets {} apart is their dedication to customer satisfaction. The company works closely with their clients throughout the entire production process, from design and prototyping to final production. Their experienced engineers provide valuable insights and expertise, helping optimize designs for the investment casting process, resulting in improved product quality and reduced manufacturing costs.In conclusion, investment castings continue to be a preferred manufacturing method for companies seeking high-quality, complex, and intricate metal components. {} stands as a leading player in this industry, combining advanced technology, skilled craftsmanship, and a customer-centric approach to deliver investment castings that meet the highest standards. With their commitment to innovation and continuous improvement, {} is well-positioned to meet the evolving demands of the ever-changing manufacturing landscape.
Aluminum Die Casting Process: What You Need to Know
Aluminum Die Casting ProcessAluminum die casting is a manufacturing process that is widely used in various industries to produce high-quality and intricately shaped aluminum parts. This process involves the use of a mold, called a die, into which molten aluminum is injected under high pressure to create the desired shape. The aluminum die casting process offers many advantages, including high precision, excellent surface finish, and the ability to produce complex and detailed parts with thin walls.The aluminum die casting process begins with the melting of aluminum ingots in a furnace. Once the aluminum reaches the desired temperature, it is injected into the die under high pressure. The pressure forces the aluminum to fill the entire cavity of the die, ensuring that the final part has the exact shape and dimensions as per the design specifications. After the aluminum has solidified, the die is opened, and the finished part is ejected. The part can then undergo various post-processing operations, such as machining, surface finishing, and assembly, to meet the specific requirements of the application.{Company Name} is a leading manufacturer of aluminum die castings, specializing in providing high-quality, precision-engineered components for a wide range of industries, including automotive, aerospace, electronics, and consumer products. With state-of-the-art facilities and a team of experienced engineers and technicians, {Company Name} is capable of producing complex and intricate aluminum parts that meet the highest standards of quality and performance.The company's aluminum die casting capabilities include the use of advanced die casting machines, robotics, and computer-aided design and manufacturing (CAD/CAM) software to ensure the precise and efficient production of parts. {Company Name} has the expertise to work with a variety of aluminum alloys, including ADC12, A380, and A356, to meet the specific mechanical and physical properties required for each application.In addition to its die casting capabilities, {Company Name} offers a full range of secondary processes, such as CNC machining, surface finishing, and assembly, to provide a comprehensive solution for its customers. The company's commitment to quality and reliability is demonstrated by its adherence to stringent quality control measures at every stage of the manufacturing process, from material sourcing to final inspection.{Company Name} is also dedicated to sustainability and environmental responsibility. The aluminum die casting process is inherently energy-efficient, as aluminum is fully recyclable and can be re-melted and reused with minimal loss of quality. {Company Name} has implemented various environmentally friendly practices and technologies in its operations to minimize its environmental footprint and contribute to a more sustainable future.With a focus on innovation and continuous improvement, {Company Name} is constantly investing in research and development to explore new technologies and materials, improve manufacturing processes, and expand its capabilities. The company collaborates with its customers to develop customized solutions that meet their specific needs and requirements, from prototype development to mass production.In conclusion, the aluminum die casting process is a versatile and cost-effective manufacturing method that offers numerous benefits for producing high-quality aluminum parts. {Company Name} is a trusted partner for customers seeking reliable and precision-engineered aluminum die castings for various applications. With its advanced capabilities, commitment to quality, and dedication to sustainability, {Company Name} is well-positioned to meet the evolving needs of its customers and the industry.
Get High-Quality Bucket Teeth for Your Excavator
Volvo Bucket Teeth has always been a leader in the industry when it comes to providing high-quality, durable, and reliable bucket teeth for construction and mining equipment. Their commitment to innovation, safety, and performance has made them a trusted name in the industry for over 50 years.The company's dedication to quality and customer satisfaction is evident in their extensive product range, which includes a variety of bucket teeth, adapters, and other related products. These products are designed to withstand the toughest working conditions and deliver exceptional performance, thus ensuring that Volvo Bucket Teeth is the go-to choice for customers around the world.In addition to their exceptional product line, Volvo Bucket Teeth also offers unparalleled customer service and support. Their team of experts is always available to provide assistance and guidance to customers, ensuring that they are able to find the right bucket teeth for their specific needs.One of the key features of Volvo Bucket Teeth products is their innovative design and engineering. The company continuously invests in research and development to incorporate the latest technologies and materials into their products, thus ensuring that they stay ahead of the competition and provide customers with the best possible solutions.Safety is also a top priority for Volvo Bucket Teeth. Their products are designed and tested to meet the highest safety standards, ensuring that operators can rely on their equipment to perform safely and efficiently in any working environment.Furthermore, Volvo Bucket Teeth is committed to sustainability and environmental responsibility. They strive to minimize the environmental impact of their operations and products by implementing sustainable practices and using eco-friendly materials wherever possible.In addition to their focus on product quality and customer satisfaction, Volvo Bucket Teeth is also dedicated to giving back to the community. The company has a strong corporate social responsibility program, supporting various initiatives and organizations that aim to make a positive impact on society and the environment.Volvo Bucket Teeth's commitment to excellence has earned them a stellar reputation in the industry, with customers around the world trusting them to provide reliable, high-performance bucket teeth for their equipment. Whether it's for construction, mining, or any other heavy-duty application, Volvo Bucket Teeth has the products and expertise to meet the diverse needs of their customers.Overall, Volvo Bucket Teeth is a trustworthy and dependable partner for anyone in need of high-quality bucket teeth and related products. With a strong focus on innovation, safety, and sustainability, the company continues to set the standard in the industry and remains a top choice for customers worldwide.
High-Quality Fastener Parts for All Your Needs
Fastener Parts Introduces Innovative Solutions to Meet Growing Industrial DemandThe demand for fastener parts in the industrial sector has been steadily increasing in recent years, driven by the expansion of manufacturing and construction activities globally. As a leader in the fastener industry, Fastener Parts has been at the forefront of meeting this growing demand with its innovative solutions and high-quality products.Fastener Parts is a renowned manufacturer and distributor of a wide range of fastener parts, serving various industries including automotive, aerospace, construction, and manufacturing. With a commitment to excellence and a focus on innovation, the company has established itself as a trusted partner for businesses seeking reliable fastener solutions for their diverse needs.One of the key factors driving the success of Fastener Parts is its ability to adapt to changing market trends and technological advancements. The company continually invests in research and development to create innovative products that meet the evolving needs of its customers. By leveraging the latest manufacturing techniques and materials, Fastener Parts is able to produce fastener parts that offer superior performance and durability, contributing to the overall efficiency of industrial operations.In addition to its commitment to innovation, Fastener Parts also prioritizes quality and reliability in its products. The company maintains strict quality control measures at every stage of the manufacturing process to ensure that its fastener parts meet the highest standards. This dedication to quality has earned Fastener Parts a reputation for providing dependable products that contribute to the safety and integrity of industrial applications.Furthermore, Fastener Parts takes pride in its customer-centric approach, offering personalized solutions to meet the specific requirements of its clients. The company's team of experienced engineers and technical experts work closely with customers to understand their needs and provide tailored recommendations for fastener parts that align with their goals. This collaborative approach has enabled Fastener Parts to build long-lasting relationships with its customers, fostering trust and loyalty within the industry.As the demand for fastener parts continues to grow, Fastener Parts remains committed to expanding its product range and capabilities to meet the diverse needs of the industrial sector. The company's extensive catalog includes a wide variety of fastener types, sizes, and materials, catering to the unique specifications of different applications. From standard screws and bolts to specialized fasteners for specific industries, Fastener Parts has the expertise and resources to deliver comprehensive solutions to its customers.Fastener Parts is also dedicated to sustainability and environmental responsibility in its operations. The company is actively involved in initiatives to reduce its environmental footprint and promote eco-friendly practices throughout its supply chain. By embracing sustainable manufacturing processes and materials, Fastener Parts is able to offer products that not only meet high performance standards but also contribute to a cleaner and healthier environment.Looking ahead, Fastener Parts is poised to continue its leadership in the fastener industry by staying at the forefront of technological advancements and market trends. Through a combination of innovation, quality, customer focus, and sustainability, the company is well-positioned to meet the growing demand for fastener parts and drive positive change in the industrial sector.In conclusion, Fastener Parts stands as a trusted partner for businesses seeking reliable and innovative fastener solutions. With a strong commitment to quality, customer satisfaction, and environmental stewardship, Fastener Parts is set to continue its success in meeting the fastener needs of the industrial sector. This dedication to excellence positions the company as a leader in the fastener industry and a driving force for progress in the global manufacturing and construction markets.
Discover the Advantages of Hydraulic Forging for Precision Manufacturing
Hydraulic Forging is an advanced manufacturing process that has revolutionized the way metal components are produced. By utilizing hydraulic pressure to shape and mold metal, this method offers unparalleled precision and strength, making it an ideal choice for a wide range of industries.One company that has been at the forefront of hydraulic forging is {}. With over 50 years of experience in the industry, {} has established itself as a leader in the field of metal forging and manufacturing. The company prides itself on its commitment to innovation, quality, and customer satisfaction, and has continually invested in state-of-the-art equipment and technology to meet the ever-evolving needs of its clients.One of the key advantages of hydraulic forging is the ability to produce complex and intricately shaped metal components with minimal material waste. By applying high-pressure hydraulic force to the metal, {} is able to create products with superior strength and durability. This makes hydraulic forged components highly desirable for use in critical applications such as aerospace, automotive, and defense industries.In addition to its precision and strength, hydraulic forging also offers cost savings and environmental benefits. The process requires less material and energy compared to traditional forging methods, resulting in reduced waste and lower carbon emissions. This aligns with {}'s commitment to sustainable and environmentally-friendly manufacturing practices.Moreover, hydraulic forging is capable of producing components in a wide range of sizes and shapes, from small intricate parts to large structural components. This versatility makes it an attractive option for a diverse array of industries, and {} has successfully catered to the needs of clients in sectors such as oil and gas, transportation, and construction.With the increasing demand for lighter, stronger, and more durable metal components, the market for hydraulic forged products is expected to grow significantly in the coming years. Recognizing this trend, {} has continued to invest in its hydraulic forging capabilities, expanding its production capacity and enhancing its technological expertise to meet the evolving needs of its customers.The company's dedication to quality and innovation has also been recognized through various certifications and accreditations, further solidifying its position as a trusted partner for hydraulic forging solutions. Its adherence to strict quality control measures and industry standards ensures that the products delivered to clients meet or exceed their expectations.In conclusion, hydraulic forging is a cutting-edge manufacturing process that has become indispensable in the production of high-quality metal components. With its precision, strength, cost savings, and environmental benefits, it offers a compelling solution for a wide range of industries. As a leading player in the field, {} is well-equipped to meet the growing demand for hydraulic forged products and continue to drive innovation and excellence in metal forging and manufacturing.
High-Quality Precision Forgings for Flanges: The Ultimate Guide
Precision Forgings For Flanges have quickly become a leading supplier in the forging industry. The company specializes in manufacturing forged flanges that are used in various industries such as oil and gas, petrochemical, and power generation. With a strong focus on quality and precision, Precision Forgings For Flanges has established itself as a trusted partner for customers worldwide.The company’s commitment to excellence can be seen in its state-of-the-art manufacturing facilities. Equipped with the latest technology and machinery, Precision Forgings For Flanges is able to produce high-quality forged flanges that meet the most stringent industry standards. The company’s team of experienced engineers and technicians ensure that every product meets the exact specifications and requirements of its customers.In addition to its manufacturing capabilities, Precision Forgings For Flanges also offers a range of value-added services to its customers. These include custom forging, machining, heat treatment, and testing. With a focus on customer satisfaction, the company works closely with its clients to provide tailored solutions that meet their specific needs.One of the key differentiators for Precision Forgings For Flanges is its dedication to research and development. The company continuously invests in technology and innovation to improve its products and processes. This commitment to continuous improvement has allowed Precision Forgings For Flanges to stay at the forefront of the forging industry, offering its customers the latest advancements in forged flange technology.Moreover, Precision Forgings For Flanges places a strong emphasis on quality control and assurance. The company has implemented rigorous testing procedures to ensure that every product meets the highest standards of quality and performance. This dedication to quality has earned Precision Forgings For Flanges a reputation for reliability and consistency in the industry.With a strong focus on environmental sustainability, Precision Forgings For Flanges also strives to minimize its impact on the environment. The company adheres to strict environmental regulations and standards in its manufacturing processes, while also implementing measures to reduce waste and conserve energy.As a global supplier, Precision Forgings For Flanges has built a strong network of customers and partners around the world. The company has established a solid reputation for delivering high-quality products and reliable service, making it a preferred choice for customers in various industries.In summary, Precision Forgings For Flanges has become a leading supplier in the forging industry, thanks to its commitment to quality, precision, and customer satisfaction. With a focus on innovation, research and development, and environmental sustainability, the company continues to set the standard for excellence in the manufacturing of forged flanges. As Precision Forgings For Flanges continues to grow and expand its capabilities, it remains dedicated to meeting the evolving needs of its customers and delivering unmatched value in the industry.
Innovative Multidirectional Forging Technique Creates Stronger and Lighter Metal Components
Multidirectional Forging Technology Revolutionizes Manufacturing ProcessesIn the world of manufacturing, staying ahead of the curve is essential to remain competitive in today's fast-paced market. One company that is leading the way in innovative manufacturing processes is {Company Name}. With their cutting-edge multidirectional forging technology, they are revolutionizing the way products are being manufactured.{Company Name} is a renowned industry leader in the manufacturing sector. They are known for their commitment to excellence, quality, and innovation. Their multidirectional forging technology is a testament to their dedication to pushing the boundaries of what is possible in the world of manufacturing.So, what exactly is multidirectional forging, and how is it changing the game for manufacturers around the world? Multidirectional forging is a process that involves applying force to a metal workpiece from multiple directions simultaneously. This results in a more uniform and refined grain structure in the material, leading to improved mechanical properties and a higher-quality end product.The multidirectional forging process is a complex and intricate one that requires a deep understanding of metallurgy and materials science. {Company Name} has invested heavily in research and development to perfect this process, and their efforts have paid off in a big way. The end result is a manufacturing process that produces parts and components with unmatched strength, durability, and reliability.One of the key advantages of multidirectional forging is its ability to produce parts with complex shapes and intricate geometries. Traditional forging methods may struggle to achieve the same level of precision and complexity, but multidirectional forging opens up a world of possibilities for manufacturers. This means that companies can now produce parts and components that were previously thought to be too difficult or expensive to manufacture.Additionally, multidirectional forging allows for improved material utilization and reduced waste, leading to more sustainable and environmentally friendly manufacturing processes. This is a crucial consideration for manufacturers in today's climate-conscious world, and {Company Name} is proud to be at the forefront of this movement towards more sustainable manufacturing practices.With their multidirectional forging technology, {Company Name} is helping manufacturers across a wide range of industries to achieve new levels of performance and efficiency. Whether it's in the aerospace, automotive, or medical device sectors, companies are benefiting from the advantages that multidirectional forging brings to the table.{Company Name} is not only revolutionizing manufacturing processes with their multidirectional forging technology, but they are also setting new standards for quality and reliability in the industry. Their commitment to excellence has earned them a reputation as a trusted partner for manufacturers around the world, and their multidirectional forging technology is a testament to their dedication to pushing the boundaries of what is possible in the world of manufacturing.Looking ahead, {Company Name} is continuing to invest in research and development to further improve and refine their multidirectional forging technology. They are dedicated to staying at the forefront of innovation in manufacturing, and their multidirectional forging technology is just one example of how they are leading the way towards a more efficient, sustainable, and technologically advanced future for the industry. With their multidirectional forging technology, {Company Name} is changing the game for manufacturers worldwide and setting new standards for quality and reliability in the industry.
Durable Aluminum Forging: The Key to High-Quality Metal Components
Aluminum Forging: Revolutionizing the Manufacturing IndustryIn an era where manufacturing technology is constantly evolving, one company has emerged as a leader in the aluminum forging industry. With state-of-the-art facilities and a commitment to innovation, {Company Name} is changing the way aluminum parts are produced and utilized.{Company Name} is a global leader in aluminum forging, with a focus on delivering high-quality products to customers across a wide range of industries, including automotive, aerospace, and defense. The company's advanced manufacturing facilities are equipped with the latest forging technology, allowing for the production of complex and intricate aluminum components with unparalleled precision and efficiency.One of the key factors that sets {Company Name} apart from its competitors is its commitment to research and development. The company continually invests in new technologies and processes to improve the quality and performance of its aluminum forging products. From advanced simulation software to cutting-edge forging equipment, {Company Name} is at the forefront of innovation in the industry.In addition to its technological prowess, {Company Name} also prides itself on its commitment to sustainability. The company has implemented a number of environmentally-friendly practices in its manufacturing process, including the use of recycled aluminum and sustainable energy sources. By prioritizing sustainability, {Company Name} is not only reducing its environmental impact, but also setting a standard for the industry as a whole.The benefits of aluminum forging are numerous, and {Company Name} is dedicated to helping its customers harness the full potential of this versatile material. From its exceptional strength-to-weight ratio to its corrosion resistance, aluminum is an ideal choice for a wide range of applications. With {Company Name}'s advanced forging capabilities, customers can be confident that they are receiving the highest quality aluminum components for their products.In the automotive industry, aluminum forging has become increasingly important as manufacturers seek to reduce vehicle weight and improve fuel efficiency. {Company Name} works closely with automotive OEMs to develop custom aluminum components that meet their exact specifications, delivering lightweight and durable parts that contribute to the overall performance of the vehicle.Similarly, in the aerospace and defense sectors, the demands for high-performance aluminum components are constantly growing. {Company Name} has the expertise and technology to produce complex aerospace components that meet the stringent requirements of the industry, including tight tolerances and strict quality standards.As the demand for aluminum forging continues to increase, {Company Name} is well-positioned to meet the needs of its customers and drive the industry forward. With its combination of advanced technology, commitment to sustainability, and dedication to customer satisfaction, {Company Name} is truly revolutionizing the manufacturing landscape.In conclusion, {Company Name} is a leading force in the aluminum forging industry, pushing the boundaries of what is possible with this versatile material. With its cutting-edge technology, commitment to innovation, and focus on sustainability, the company is paving the way for a new era of manufacturing excellence. Whether it's in the automotive, aerospace, or defense industries, {Company Name} is helping its customers achieve success through high-quality aluminum forging products.
How To Forge Steel: A Complete Guide
Forging Steel: The Art of Crafting Quality Steel ProductsSteel has been a vital material in various industries for centuries, with its strength, durability, and versatility making it an essential component in many applications. From construction and manufacturing to automotive and aerospace, steel plays a crucial role in ensuring the quality and performance of products and structures. As such, the process of forging steel is an art that requires precision, expertise, and state-of-the-art technology.One company that has mastered the art of forging steel is {}. With a rich history that spans over a hundred years, {} has established itself as a leading manufacturer of high-quality steel products. From raw steel to finished products, {} is dedicated to delivering exceptional quality and performance across its extensive range of offerings.The process of forging steel involves shaping and molding the material into desired forms and dimensions through controlled heating and pressure. This process not only enhances the strength and durability of the steel but also refines its grain structure, resulting in improved mechanical properties. {}'s state-of-the-art facilities and advanced forging techniques enable the company to produce steel products that meet the highest standards of quality and performance.At the heart of {}'s forging process is a team of highly skilled and experienced craftsmen who possess a deep understanding of metallurgy and the intricacies of forging steel. These craftsmen work tirelessly to ensure that every piece of steel that leaves the {} facility is of the highest quality, meeting the specific requirements and demands of its customers.From steel bars and tubes to custom-designed components, {} offers a wide range of forged steel products that cater to various industries and applications. Whether it's for construction, machinery, or transportation, {}'s steel products are designed to meet the toughest challenges and deliver outstanding performance in the most demanding environments.In addition to its forging capabilities, {} is also committed to sustainable and eco-friendly manufacturing practices. The company's focus on environmental responsibility extends to its entire production process, from sourcing raw materials to the final product. By integrating sustainable practices into its operations, {} ensures that its steel products not only meet the highest quality standards but also adhere to strict environmental regulations.As a testament to its dedication to excellence, {} has earned numerous certifications and accolades for its commitment to quality, safety, and environmental stewardship. These accolades serve as a testament to {}'s position as a trusted and reliable partner for companies seeking high-quality steel products for their critical applications.{}'s relentless pursuit of excellence and innovation has propelled the company to the forefront of the steel forging industry. Its unwavering commitment to quality, combined with its extensive experience and expertise, has positioned {} as a leader in delivering premium forged steel products to its customers, setting the standard for excellence in the industry. With a strong focus on precision, performance, and sustainability, {} continues to raise the bar for the forging steel industry, setting new benchmarks for quality and reliability.In conclusion, the art of forging steel is a delicate balance of precision, expertise, and innovation, and {} has mastered this art like no other. Through its unwavering commitment to quality, sustainability, and customer satisfaction, {} has established itself as a leading manufacturer of high-quality forged steel products, setting the standard for excellence in the industry. With a rich history and a relentless pursuit of perfection, {} is poised to continue delivering exceptional steel products that meet the evolving needs of its customers and the industries it serves.
High-quality metal parts for industrial use
Metal Parts, a leading manufacturer in the field of industrial equipment, has announced the launch of their latest product line which is set to revolutionize the industry. The company, which was founded in 1995, has been at the forefront of producing high-quality metal parts for a wide range of applications including automotive, aerospace, electronics, and more. Their commitment to innovation and excellence has made them a trusted partner for many businesses around the world.The new product line, which consists of various metal parts including components and assemblies, is designed to meet the demands of modern industrial applications. The parts are made from high-grade materials such as stainless steel, aluminum, and titanium, ensuring durability and reliability in the most demanding environments. With state-of-the-art manufacturing facilities and a team of highly skilled engineers, Metal Parts is able to deliver precision-engineered components that meet the strictest quality standards.One of the key features of the new product line is its versatility. The parts are designed to be used in a wide range of applications, making them suitable for a variety of industries. Whether it's for automotive components, electronic enclosures, or aerospace assemblies, Metal Parts has the capability to deliver tailored solutions that meet the specific needs of their customers. This flexibility sets them apart from their competitors and makes them a valuable partner for businesses looking for reliable metal parts.In addition to their commitment to quality and versatility, Metal Parts is also dedicated to sustainability. The company has implemented environmentally friendly practices in their manufacturing processes, ensuring that their products have minimal impact on the planet. By using recyclable materials and reducing waste in their production, Metal Parts is contributing to a greener, more sustainable future for the industry.To ensure the success of their new product line, Metal Parts has invested heavily in research and development. They have a team of experts who are constantly exploring new materials, manufacturing techniques, and designs to stay ahead of the curve. This commitment to innovation allows them to deliver cutting-edge solutions that meet the evolving needs of their customers.Metal Parts has also made significant investments in their infrastructure to ensure that they have the capacity to meet the growing demand for their products. Their state-of-the-art manufacturing facilities are equipped with the latest technology and equipment, allowing them to produce high-quality metal parts at scale. This ensures that they can support the needs of their customers, whether they require small batches of components or large volumes of assemblies.With their track record of excellence, commitment to sustainability, and dedication to innovation, Metal Parts is well-positioned to lead the industry with their latest product line. Their ability to deliver high-quality, versatile, and sustainable metal parts makes them a valuable partner for businesses across various sectors. As they continue to grow and expand their product offerings, Metal Parts is poised to make a lasting impact on the industrial equipment market.